TOPBAND
Shenzhen Topband Battery Co.,Ltd. was established in 2006, and is a wholly-owned subsidiary of Shenzhen Topband Co. Ltd (002139.SZ) which is the world’s leading intelligent control solution provider. Headquartered in Shenzhen, Guangdong province. It has six production bases in Shenzhen, Huizhou, Nantong, Taixing, Vietnam and India. With its focus on lithium-ion products, the company is able to conduct independent R&D and manufacturing in the three core areas of cells, BMS and system integration to ensure stable and reliable product performance. The company strives to be a first-class and reliable international provider of lithium products to create low-carbon life for the customers, and its products are widely used in energy storage and light motive power fields worldwide.
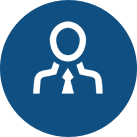
- Background
Got listed in 2007 (002139.SZ)
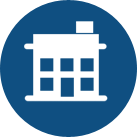
- Location
Headquarters and R&D Center:Shenzhen Production Base:Huizhou,Taixing,Shenzhen,Nantong,India,Vietnam
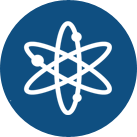
- Capacity
4.0GWh
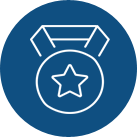
- Certification
ISO9001, ISO14004, IATF16949, ISO14001, UL, UN38.3, TUV